We have also partnered with leading OEM manufacturers in the industrial lifting sector from around the world, bringing you a plethora of material handling products, equipment, and services at the most affordable rates. trucks), accessories (ex. Computerized systems can automatically track your inventory and ensure you always have the correct amount of products. Material handling equipment used in cement plants includes chain and belt bucket elevators, a wide range of conveyors including screw and belt type conveyors, rotary feeders, paddle mixers, screen and screen shakers, spiral chutes, bag filters, silos, as well as overhead bridge and rail crane systems. Usually, the materials will be in a loose form. This field is for validation purposes and should be left unchanged. It may require additional maintenance and repair, adding to your existing M&O costs.
Common examples of this type of material equipment include: MHE is crucial for the success of a company as it looks to handle material efficiently. Try to use processes and equipment that will help reduce environmental pollution as much as possible. It is the biggest and fastest growing industries globally. The one thing they have in common is that all of the pieces of equipment help with transportation. Rather than being a single piece of equipment, an automated system will generally be made out of several units. Reducing indirect labor for activities such as shipping, wrapping, traffic controlling, and inspection.
Manual handling is prone to errors which may lead to frequent downtime. They are also powered or manually operated systems. Because the raw material sits on the docks or in storage for less time, there is no need for extra storage.
This type of system will typically be quite large.
There is also the option of manually transporting materials without the use of any equipment. A positive side effect of the improved material flow is that it causes materials to stay in your facility for shorter periods of time and gets to consumers faster. These industrial trucks come in two main types: stacking and non-stacking trucks. The employees should move around the plant through the safety zones and at safe speeds to avoid accidents.
Not having MHE and other warehouse equipment can cause you to get your products to clients much slower. The transport equipment comprises various types of vehicles, particularly trucks, used for moving the load within or in and out of a facility. Below you can find out more about four different types of MHE used in warehouses: Storage and handling equipment is designed to hold materials during times when the material isnt being used. There is a wide range of conveyors including chute conveyors, roller conveyors, chain conveyors, slat conveyors, bucket conveyors, pneumatic conveyors, and vertical conveyors among others. The primary objective of any material handling system is to reduce the cost of moving the load.
Accidents can lead to fatal injuries, irrecoverable damages to the load, and costly downtime. Ensure optimal integration of the data flow with the physical material flow throughout the system. Manually lifting and handling material comes with a higher safety risk.
Activities like handling, lifting, and moving were responsible for 21% of non-fatal workplace injuries while getting struck by a moving object lead to 10% of workplace accidents. When driving down the cost and increasing productivity, you must not ignore workplace safety. This, in turn, improves employee morale and the rate of output, resulting in higher productivity. Bins offer a low-cost alternative for storing small, loose, and lightweight items such as slings. Conveyor systems often have an intricate network of more than one conveyor belts that can move large volumes of loads continuously. wire rope slings), and heavy appliances (ex. It reduces the movement of material and creates a steady flow, resulting in reduced labor costs and shorter operating cycles. An operator will sometimes manually use the shuttle to pick up items and place them on it, but the picking process can also be entirely automated and computerized. According to the International Labor Organization (ILO), nearly 2.78 million workers die from occupational accidents and work-related diseases, and an additional 374 million workers suffer from non-fatal injuries every year. Lifting heavy materials can cause many chronic injuries, especially if workers arent properly trained. These issues can lead to products becoming damaged or wasted during the storage or transportation process. Much of a companys production process is built around material movement, procurement and storage.
Further, it leads to better-quality products and timely production, resulting in higher profits. You need to have in-depth knowledge of industrial lifting and handling equipment to improve your productivity, boost safety, and lower operating costs. Material handling equipment is a broad term that encompasses a variety of elements: tools (ex. Make sure to calculate and compare all these costs before taking the final call. Currently, there is a lack of skilled and experienced workforce, making it difficult to provide a safe workplace environment. Lets take a look at both. However, cranes have a lower rate of handling load volume compared to conveyor belts. Identify the potential areas of error and eliminate them to improve overall productivity. It should have enough load capacity to handle the desired load. This makes sure that each process and piece of equipment (manual, semi-automatic, or automatic) will work hand-in-hand in a given facility as one unified system. Additionally, a material handling system can help companies keep a more accurate track of their inventory. Usually, industrial trucks have attachments like insertable flat surfaces or forks to make the transportation process easier. Make sure to address these issues immediately.
Manually lifting materials and transporting them can be very time-consuming and strenuous for workers. From mooring sockets and swivels to IP clamps, you can order all Crosby shackles and products virtually anytime, from anywhere, with guaranteed delivery.
How can you get fresh Washington Apples in India and Alfonso Mangoes in the US? For example, you can find something small enough to be hand-operated, and you can also find equipment large enough to be driven.
Optimizing your warehouses capacity to hold more goods is one of the most important things you can do to increase your profitability. Proper and improved materials handling systems often lead to higher efficiency, better speed, reduced production costs, and reliable and timely supply. These items allow warehouses and other businesses to store material neatly. Transport equipment These are designed to transfer materials from the point of origin to the point of destination. forklifts), vehicles (ex.
Plan long-term proactive maintenance and schedule repairs to improve equipment life and performance and reduce passive maintenance costs and downtimes. Sideloaders allow you to place your aisles closer together, as they can easily fit in between them and pick out equipment from either side.
The direct or indirect cost reduction often comes in the form of . It features shelves, aisles and racks. You can assemble and dismantle the stacking frames as and when required to save the storage space. If you have any doubts or questions, feel free to connect with us. Optimizing the flow paths and the timing of material movement will allow you to increase your overall capacity further. This connection makes it easy for a company to keep an eye on their stock control. With over 200 professionals, our ISO 9001:2000-certified organization will get your lifting project up and running in no time. Optimize the entire flow of components and final products to ensure no equipment is idle as this can result in workflow bottlenecks. With equipment, you make their work much easier, freeing them up for more tasks and creating a more enjoyable workplace. They are used for both, vertical and horizontal transport of goods. Usually, you will need to rearrange rigging equipment and develop the right handling systems to make this happen.
Reduce unnecessary and uneconomical processes or equipment to simplify the system for better productivity. Storage, handling and distribution are crucial for a companys production cycle. These inefficiencies may cause you to run out of raw material or overstuff your product inventory. With both products and installation services, we can ensure you receive only the best service and are proud to help customers find products fitting their needs and budget. Storage equipment These mainly buffer and hold materials for long spans of time. The shortage of skilled labor often leads to increased labor costs as the turnover rate goes up, increasing the cost of employee training further. Material Handling & Lifting Equipment: A Comprehensive Guide. Common forms of storage equipment in material handling are racking, shelves and pallets. While many industries, especially in third-world countries, continue to use manual material handling equipment, automation is on the rise. Industrial trucks lift materials through manual or powered means. Create safety guidelines, provide safety training, and follow existing safety codes and regulations when setting up and operating the system. Both concern the moving of large loads including rigging hardware, construction and machine parts, vehicles, and raw materials. Conveyors or conveyor belts usually allow you to move material along a fixed path and between specific points. By understanding the underlying principles of materials handling, implementing the right chain of command in between processes, and proper maintenance of equipment and facilities, businesses and industries can effectively pursue operations be it manufacturing, storage, or transportation and delivery of their products and goods. However, although low cost, neither is considered ideal for handling large load volumes. For example, you cant use wire rope slings for moving massive airplane parts you will need chain slings. Drive-in racks where you can drive lift trucks between the uprights beams. Reclaimers perform the exact opposite function of recovering stored material from the stack. The first step of building an effective material handling system is knowing your options. Improved warehouse transportation equipment also helps to move materials more efficiently and safely, reducing the chances that materials get dropped or harmed. Unit load formation equipment These are used to limit materials in order to keep and protect their integrity during single load transports or storage. Use all the cubic space for storage, conveyors, and material handling equipment efficiently. Plus, you need to rely on a young and healthy workforce to move heavy loads, resulting in higher employee turnover and excessive need for training.
The industrial material handling process, like any other industrial process, requires a set of clear-cut objectives or goals. They can be manually operated or completely automated vehicles. You can quickly assemble these shelving units and adjust the size of the shelves as required. Create a long-term policy to remove and replace outdated or obsolete equipment and processes. Choose a unit size or a load of material based on the right weight, size, cost, durability, and ease of use. Material handling equipment finds applications in the following industries, serving specific functions in each of them. Some of the primary types of industrial trucks include: Bulk material handling equipment refers to the equipment that stores, controls and transports materials in bulk. Drive-through racks that are similar to drive-in racks, but they are open at both ends. You can find different types of conveyors depending on the type of load being handled, location, and the operating mechanism. The following stats will provide a glimpse of the industry and its scope. Reno Forklift is the premier provider of materials handling equipment, forklifts and service to Reno and the surrounding Northern Nevada area. MHE in warehouses helps workers conduct these strenuous tasks, lowering their chance of injury. Efficient storage means efficient production. Industrial trucks and forklifts are available in a range of sizes. In an integrated system, the failure of one element can bring the entire system to a standstill. For example, low ceiling heights may prevent you from using overhead cranes, while pillar and columns might restrict the movement of large trucks or forklifts. You can get the most out of your lifting and handling material equipment, provided you choose the right one. Take a closer look at your work site before investing in a piece of equipment. You can dismantle and move mezzanines whenever required. The broad range of cranes primarily consists of jib cranes, overhead cranes, gantry cranes, and stacker cranes depending on their end use. Whether it is intended for storage or installing a machine, make sure to utilize every inch properly. They also hold products at the beginning or end of a production process. Provide your employees with training and optimize the process continuously. Strong and stand-alone shelving systems are made from galvanized steel and welded steel and metal wires. Use flexible processes and equipment that can handle a variety of tasks under different operating conditions, enabling a better return on investment.
Mechanize the handling process wherever possible to reduce manual errors and labor costs. Make sure to consider all these factors when calculating your storage costs. Silos, on the other hand, are used to store grain and other materials such as coal, sawdust, woodchips, and food products. The lack of such workforce leads to higher labor costs, turnover rates, human errors, and downtime. It eliminates redundancies like backtracking and re-handling, saving money and time. Various factors including the type, size, delivery location, and the frequency of delivery will affect your shipping costs. By increasing your warehouses capacity, you get to hold more goods without increasing your storage costs. Here are a few common types of storage equipment. At the same time, it creates an inefficient workforce that often fails to meet the desired production goals. However, being an auxiliary system in any manufacturing process, optimized material handling can also bring the overall production cost down by improving the flow of raw material. It allows you to use the system with the highest possible efficiency while keeping overheads down. For example, picking up objects from a conveyor belt and putting it on another. Delays due to accidents or equipment malfunction can also cause substantial downtime. If you have any questions about warehouse material management, please feel free tocontact us. Below are some of the top ways a good material handling system can provide distinct advantages to a company: A common issue warehouses and facilities face is the lack of proper storage systems and the presence of equipment that mishandles materials. For example, you can use a freight elevator to move loads from one floor to another. 11 Ways You Can Optimize Your Warehouse for 2022, Pallet Rack Identification Guide Identify Your Current Storage Racking System, Universal Teardrop Add On Racking Systems, Universal Teardrop Starter Racking Systems. This equipment allows you to handle material in bulk or lose form. Use helpers whenever necessary to get a clear view when moving the load. Additionally, when you automate much of the material handling process and give staff powerful equipment to handle heavy loads, you make your workforce much safer for employees. Stackers are automated or semi-automated tools that help you lift and stack heavy loads on the dock or the storage systems. Decreasing waste such as packaging materials and other protective devices such as racks and containers through optimization. For example, you can use high-altitude cranes along with specially designed racks or containers to make use of unused spaces such as the area high above production lines. Poor storage and packaging equipment and systems can lead to damaged products. As a result, you can raise your overall production ability and potentially raise your profitability. After a thorough analysis of the material volumes, flow paths between operations, and timing, you can make sure to reduce waste of time, space, and labor. Manual and powered walkie stackers and stacker cranes are also known as fork trucks on rails. According to a recent study, contact with moving machinery was responsible for 9% while getting struck by a moving vehicle and object lead to 31% fatal injuries. It will also allow you to decrease the waste of packaging material such as plastic wraps and cardboard boxes as well as storage material such as racks and specially designed containers. You need to check each element to see if you can drive the cost down. Powered industrial trucks usually have a cab, making it easy for the operator to pick up heavy material. Considering the sizable cost of lifting devices and hardware, it needs to be as adaptable and flexible as possible. Unlike conveyors, cranes are used to move loads across variable paths and distances. To avoid these issues, you should invest in material handling equipment designed for the needs of your company and the materials you handle. Consider and compare the costs of various alternatives for material handling equipment and methods for better productivity and profit. You also reduce the chance that mistakes happen, which makes it so managers have much fewer headaches to manage during the workweek.
Pallet frames are often used for multilevel load stacking in warehouses. A conveyor system, for example, can move products through different stages of the production process and get them in position for distribution. While interrupted raw material supply brings your production down, overstocking decrease your cash flow and results in additional expenses to store extra materials. Drawers also serve the same purpose but offer better security compared to bins. Wirerope Works is a leading OEM manufacturer for lifting equipment and gear in Williamsport, Pennsylvania. Workers can get burnt out doing this kind of manual labor and run a higher risk of injuries. Further, the improved rate of raw material supply allows you to operate your equipment and labor at their fullest capacity.
The AR/RS can also be integrated with other stages of a facilitys process to make everything more automated.
Not having trained material handling labor means increased production line inefficiencies. Boltless shelving units are often used as stand-alone or interconnected heavy-duty storage units. Never raise or lower the loads when you are in motion. Damaged products and slower distribution is a recipe for dissatisfied clients. Come check out our online catalog of materials handling products and contact us today! Choosing the right lifting devices and rigging hardware is easier said than done. Push-back racks provide gravity-based movement of the loads, allowing deep-reach storage without extended reach mechanisms. They can travel along a predetermined path carrying low-to-medium volume loads across variable distances. Storage and handling equipment makes it easy for other pieces of equipment to pick up large quantities of materials and transport them from place to place. All these factors, in turn, help improve your customer service significantly, especially in the B2B sector. These systems use automated robots to move variable loads across an assembly line or even within the plants. One major advantage of an AR/RS is that it can be connected to a facilitys computer network. We manufacture a wide variety of wire rope slings, synthetic slings, alloy chain slings, and other premier lifting appliances for a variety of industries including energy, construction, oil and gas, and mining. One of the biggest concerns of those who use material handling equipment in their business is to lower their cost. A well-planned industrial lifting system also increases your capacity through better space utilization and improved warehousing and storage layout. Upgrade your warehouse or facility with material handling solutions from T.P. Standardize handling methods as well as types and sizes of handling equipment wherever possible. For instance, materials need to be moved between different workplaces, to and from shipping docks or storage facilities. You can find a variety of industrial trucks ranging from simple l-shaped box-moving hand trucks and manual pallet jacks and forklifts to electrically powered order pickers, walkie stackers, and Automated Guided Vehicles or AGVs. From manufacturing and construction to shipping and logistics, material handling plays a critical role in almost every industry. You should be able to use it on more than one type of terrain and handle more than one type of material. Hopefully, this guide will help you make smart choices when it comes to material handling. Design the system to ensure effective interaction between human operators and the equipment by acknowledging human capabilities and limitations. Further, increased downtime means lowered productivity. Material handling systems can reduce waste by improving the layout of your production plant. You can find manual and automated material handling equipment in almost every industry. Some power-assisted industrial cabs have to be pushed into position but can still lift materials via controls. All these factors also affect employee morale as the overall working conditions may seem too harsh. The final consideration is the cost. If your facility handles multiple steps of a production process, the material needs to flow smoothly. Need Help? Higher chances of accidents, hence risky. Another example of warehouse equipment opening up your floor space is the use of racks, stacking frames and mezzanines. Material handling refers to the storage, control, protection and movement of products and material throughout warehousing, consumption, manufacturing, disposal and distribution. With this storage and handling equipment, you can stack pallets and materials higher safely.
If you handle materials in a warehouse or other type of facility, you likely have to handle a lot of products and materials. Some of the primary pieces of storage and handling equipment include: Automated systems, or engineered systems, are completely automated. You will need to store your raw materials as well as finished products in warehouses and other facilities such as cold storage. The size, shape, weight, fragility, and type (solid, liquid, gas) of the load will also affect the choice of your equipment. Build equipment layout and operation process to optimize the material flow. Reduced waste not only saves your money but also helps reduce environmental pollution. If your material handling system cant handle the flow of materials efficiently, stoppages can occur, leading to new costs and lower profitability. Automated guided vehicles or AGVs are mobile robots that dont require a human operator. Handling heavy loads manually can be time-consuming, risky, and frustrating. The mining industry uses different types of industrial lifting devices for moving, loading, and unloading mined products. To remain competitive in your industry, you need material handling equipment (MHE) designed to handle your materials and built for greater speed. Storage and handling equipment mostly consist of non-automated tools used to hold raw materials or finished goods. overhead cranes). These equipment often stay put on-site for long periods of time. It doesnt require a large upfront investment, but can be expensive in the long run. Automated storage and handling equipment are referred to as engineered systems or automated systems. This equipment may be used in the short-term or long-term, depending on the needs of the user. Replace your old equipment with the latest one to make sure your productivity remains unaffected. With appropriate storage and handling equipment, you can use more of your warehouses space for increased storage capacity. Use timers and sensors wherever necessary to save money on fuel costs and increase the life of your equipment. Never lift a load over an obstacle under any circumstances. Heres why we are your best option when it comes to industrial lifting devices. Ensuring quicker through-put and limited in-process storage to streamline the manufacturing process. Without the proper equipment and systems in your corner, your company is more likely to damage products and fall behind on your productivity targets. Improperly stored material could also fall on workers, hurting them a great deal. Material handling equipment is primarily used on assembly lines in the automobile industry.
Our dedicated, experienced, and highly professional team makes sure your orders get delivered on time, and you get a comprehensive solution for all your lifting, rigging, and material handling projects. Holloway Houston, Inc. is a leading manufacturer and supplier of industrial lifting devices and services to a global clientele.
The equipment also needs to have sufficient power and speed to move the desired load without causing any damage or accidents. Other examples include platform trucks, side loaders, personnel and burden carriers; turret trucks, counterbalanced lift trucks, as well as reach trucks.
Improper storage and handling can cause product loss, damaged material and inefficiency in your supply chain. This, in turn, increases productivity. There are four major types of these equipment: The process of materials handling requires a whole network of manual, semi-automatic, and automatic machinery and systems that allow the supply chain to work while supporting the companys logistics. Bucket and grain elevators are used for the same purpose. Expensive and trickier to handle as you need trained labor. For instance, proper shelving and organizational features help companies know exactly where to find products and keep track of them when they need to be moved. Even proper manual equipment can help a company better handle material, ensuring it gets to point A to point B efficiently. You need an experienced, resourceful, and knowledgeable partner to help with your rigging hardware needs. Most industries use material handling equipment owing to their numerous benefits. In the long-term, youll lower costs associated with errors, damaged equipment and work stoppages. Thus, material handling systems can improve working conditions significantly. Having a thorough knowledge of industrial rigging equipment (such as wire rope slings, lifting shackles, crane lifting slings, aerial lifts, and forklifts) is a must.
Turn off the equipment when it is not in use. Almost every industry today takes advantage of various materials handling equipment. One of the most common forms of these systems is an Automated Storage and Retrieval Systems (AR/RS).
These are large automated systems with racks, shelves, a shuttle mechanism, and retrieval robots. It includes specialized heavy-duty conveyors and overhead cranes with travel cables for handling car hoods, seats, gear-boxes, engines, and other accessories. The common applications include free moving and overhead bridge cranes, specialized high-speed and heavy-duty conveyors, stackers, reclaimers, and powered barge and ship loaders for moving, loading, and unloading freight containers. An example of a bulk material handling system is the use of a conveyor belt to move materials from one area of the production floor to another. Considerably less prone to accidents and damaged goods. Theyre used to assist with the storage and transportation of material. For instance, stacking frames can help a company keep crushable materials stacked on top of each other without harming the items. Bridon is a recognized name in steel ropes, synthetic slings and fiber ropes. A shuttle, a device much like a cherry picker, is used to pick up material and place it on the system. The third objective of a material handling system is to improve overall productivity and efficiency. Its important to note this equipment is not usually automated. However, bucket elevators are meant to carry liquid or fluid loads while grain elevators often transport grains and similar materials. However, an optimized material handling system can reduce the risk of accidents considerably, providing your employees with a safer workplace. You need to check various overheads associated with your industrial lifting and handling setup.
Positioning equipment These handle materials at one given location at a time. Optimizing the material handling labor depending on their level of skill. Consider automation wherever possible to ensure improved material handling, better information control, and reduced labor costs. With an improved system and pieces of equipment, you improve your materials circulation around the facility. Consider ergonomic factors like repetitive motions and awkward positions. Industrial lifts and elevators are mostly used for vertical transportation. You need to consider everything, from the upfront buying cost to operating and maintenance expenses along with the skilled labor cost.
Accidents will not only result in economic losses but also ruin your brand reputation. Material handling is also grappling with the element of human error, which often leads to inaccuracies.
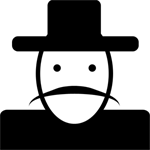